From compact skid steers and mini-excavators to massive dozers and off-highway trucks, construction...
How HVAC-R Systems Keep Mining Vehicles Safe, Efficient, and Operational
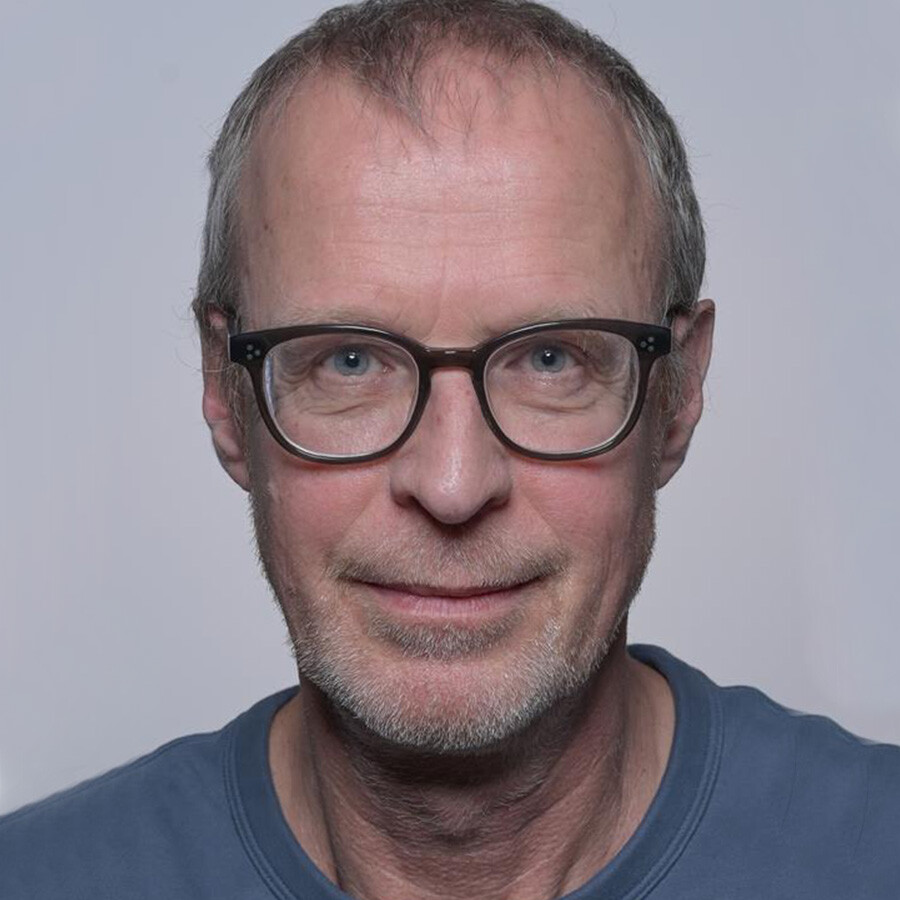
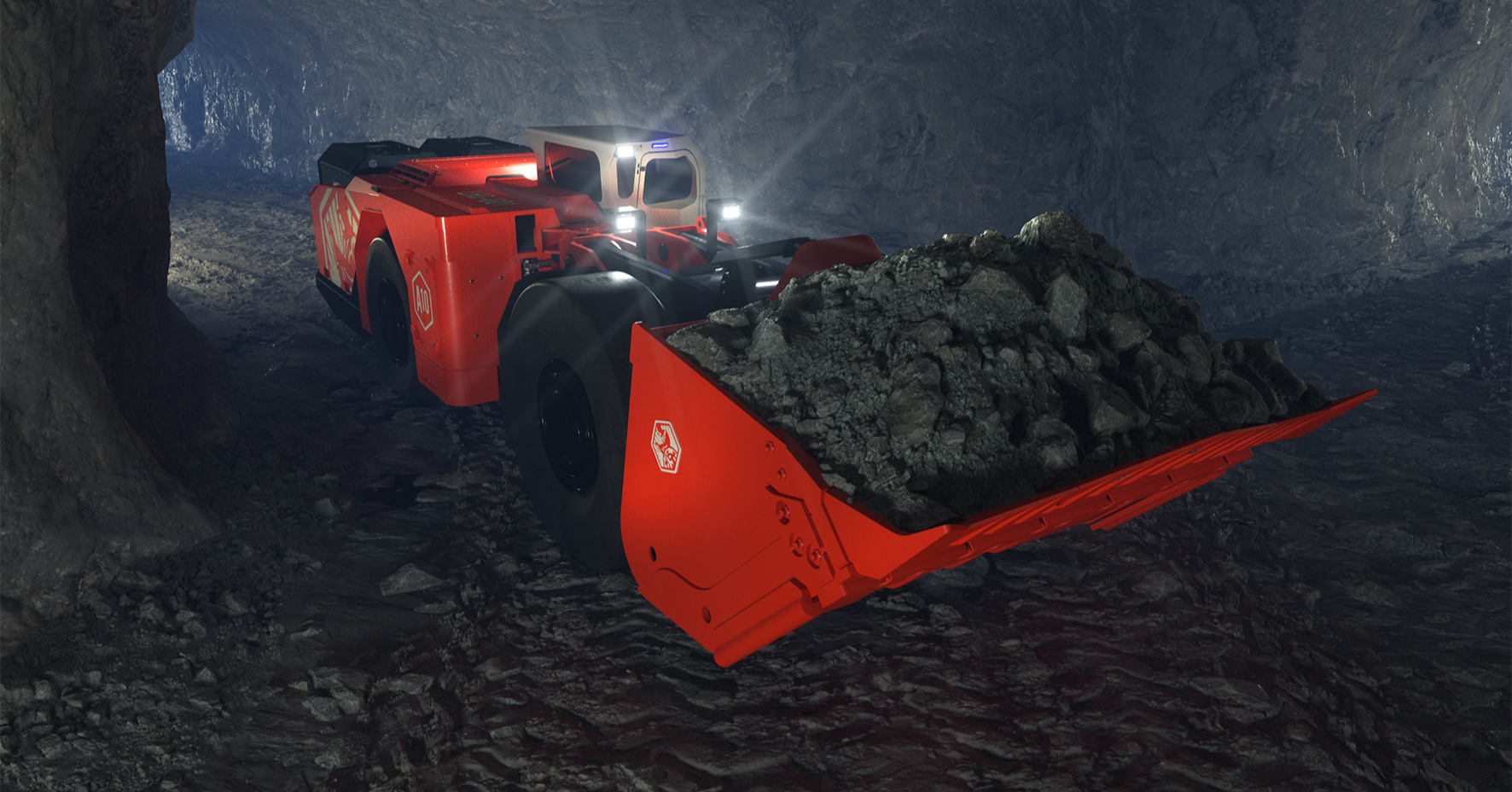
Mining is one of the most demanding industries, with extreme environments that push both equipment and operators to their limits. Due to extreme heat and dust, mining operations rely on innovative HVAC-R solutions to keep workers safe and equipment in top working condition.
Extreme Challenges of Mining Environments
Underground or above ground, mining vehicles like drill rigs, mechanical haul trucks, hydraulic mining excavators, dozers, electric rope shovels, and wheel loaders must endure searing heat, dense dust, and constant vibrations. Popular mining equipment manufacturers like Sandvik, Epiroc, Komatsu, and CAT rely on the industry’s most rugged HVAC-R systems to ensure safety, productivity, and the longevity of their fleets.
Heat and Temperature Variability
Underground mines can reach scorching temperatures due to a combination of geothermal heat, machinery, and human activity. Temperatures underground increase by 72–87°F (22–30°C) per mile of depth, with some mines reaching 125–130°F (51–54°C) on average. Heat stress is a significant risk for workers in these conditions, affecting concentration, dexterity, and decision-making. Studies show that the highest accident rates occur when temperatures exceed 80°F (27°C).
Above-ground mining vehicles face less intense heat but are subject to dust, vibration, and varying weather conditions, creating challenges for HVAC systems to maintain consistent cabin temperatures.
Dust and Air Quality
Mining operations generate significant amounts of airborne dust, which poses risks to both operators and equipment. Dust infiltration affects vehicle HVAC performance and reduces air quality in cabins, increasing the risks for drivers. Regulatory standards like ISO 23875 mandate systems that monitor and control cabin air pressure and CO2 levels to safeguard workers.
Humidity and Corrosion
In underground mines, high humidity is a major contributing factor to both equipment degradation and operator safety risks. Groundwater flowing through hot rock formations adds to the moisture in the air, causing corrosion of metal vehicle components.
The Role of HVAC Systems in Mining Vehicles
Global regulations enforce strict guidelines for air quality and temperature control in mining operations. For example, Canadian laws restrict work in underground mines at temperatures exceeding 80°F (27°C), with similar restrictions in many other countries. With a focus on worker safety and operational efficiency, MCC’s HVAC systems are designed to meet and exceed these requirements with solutions tailored specifically for global mining operations.
Safety and Comfort for Operators
Mining vehicles often operate in confined spaces with limited visibility and intense heat. HVAC systems create a livable environment by regulating cabin temperature, reducing humidity, and ensuring filtered air free of dust and harmful particles. Advanced filtration technologies, such as HEPA filters, are often employed to meet stringent safety requirements.
Operational Efficiency and Equipment Protection
Mining vehicles generate immense heat during operations. For example, drilling operations can require 300 kW of cooling capacity just to manage hydraulic oil temperatures. However, this energy-intensive requirement means that HVAC energy savings (around 5 kW) are not a primary concern. Due to the high power demands of these machines, they cannot operate solely on battery power. Instead, batteries are used for transport between work sites, while HVAC systems run on plug-in power once the machines are in operation.
Above ground, the constant vibrations from machinery like Sandvik and Epiroc drill rigs add another layer of stress on HVAC components, requiring durable systems designed for rugged conditions.
How to Ensure Worker Safety and Drive Productivity with Reliable HVAC Systems
Operators working in safe, comfortable environments are more alert and less prone to fatigue or heat-related accidents. Additionally, robust HVAC systems protect vehicle components from overheating and dust, reducing maintenance costs and extending the lifespan of mining equipment. To meet and exceed industry standards, MCC’s innovative HVAC solutions for mining address all of the challenges typical to the mining industry, while looking to the future for new and innovative ways to increase productivity and safety.
Cutting-Edge Filtration and Air Quality Control
MCC’s air quality control systems integrate cabin overpressure with CO2 sensors, meeting ISO 23875 requirements. These systems actively monitor and regulate air quality to protect operators. Modular cyclone filtration systems, which can be retrofitted or integrated into HVAC units, offer enhanced dust management, even in the harshest environments.
Corrosion-Resistant Designs
MCC’s HVAC systems are built to endure the high humidity and corrosive conditions found in underground mines. To combat corrosion, pre-coated aluminum fins, copper fins, and stainless steel housings provide long-term durability and reduced maintenance needs.
Energy-Efficient Thermal Management
Although electric and hybrid mining vehicles are not yet widespread, MCC has developed HVAC systems tailored to these emerging technologies. These systems optimize battery thermal management, ensuring efficient energy use and longer operating hours for electric vehicles in remote or underground locations.
Ready to explore more of MCC’s cutting-edge HVAC technologies? Contact us today.
February 19, 2025