Side-by-side vehicles are built with the power and durability to go almost anywhere. Whether...
Inside the Cab: How HVAC Systems are Engineered for Different Construction Vehicles
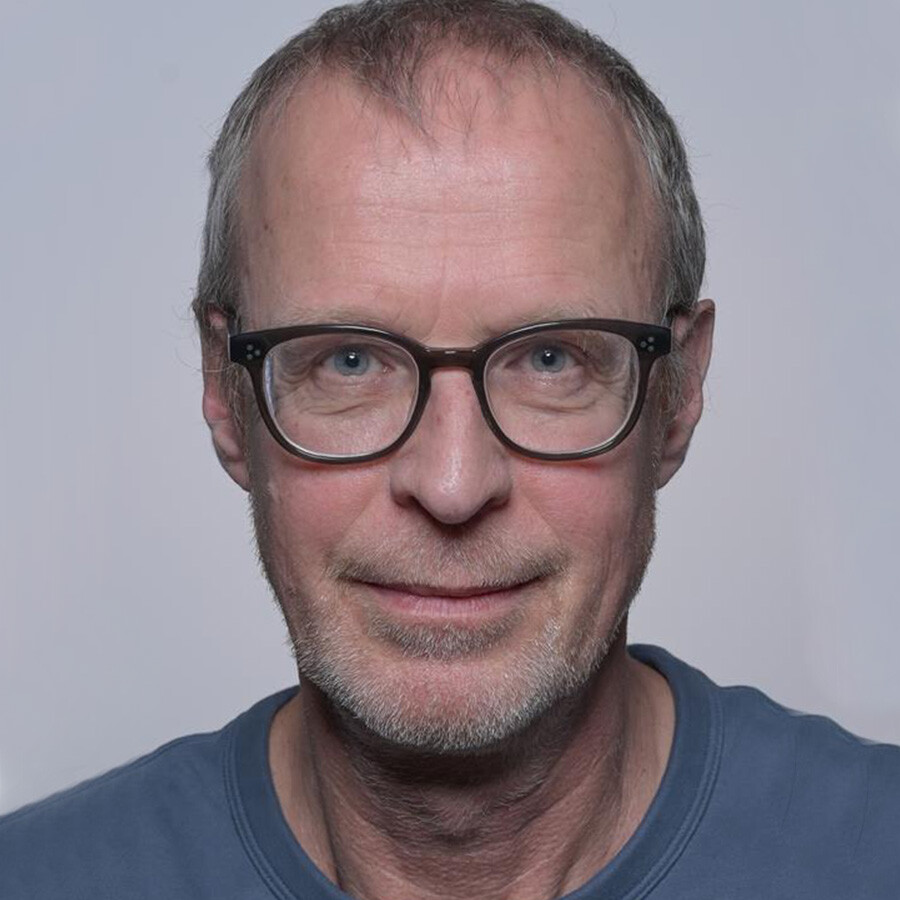
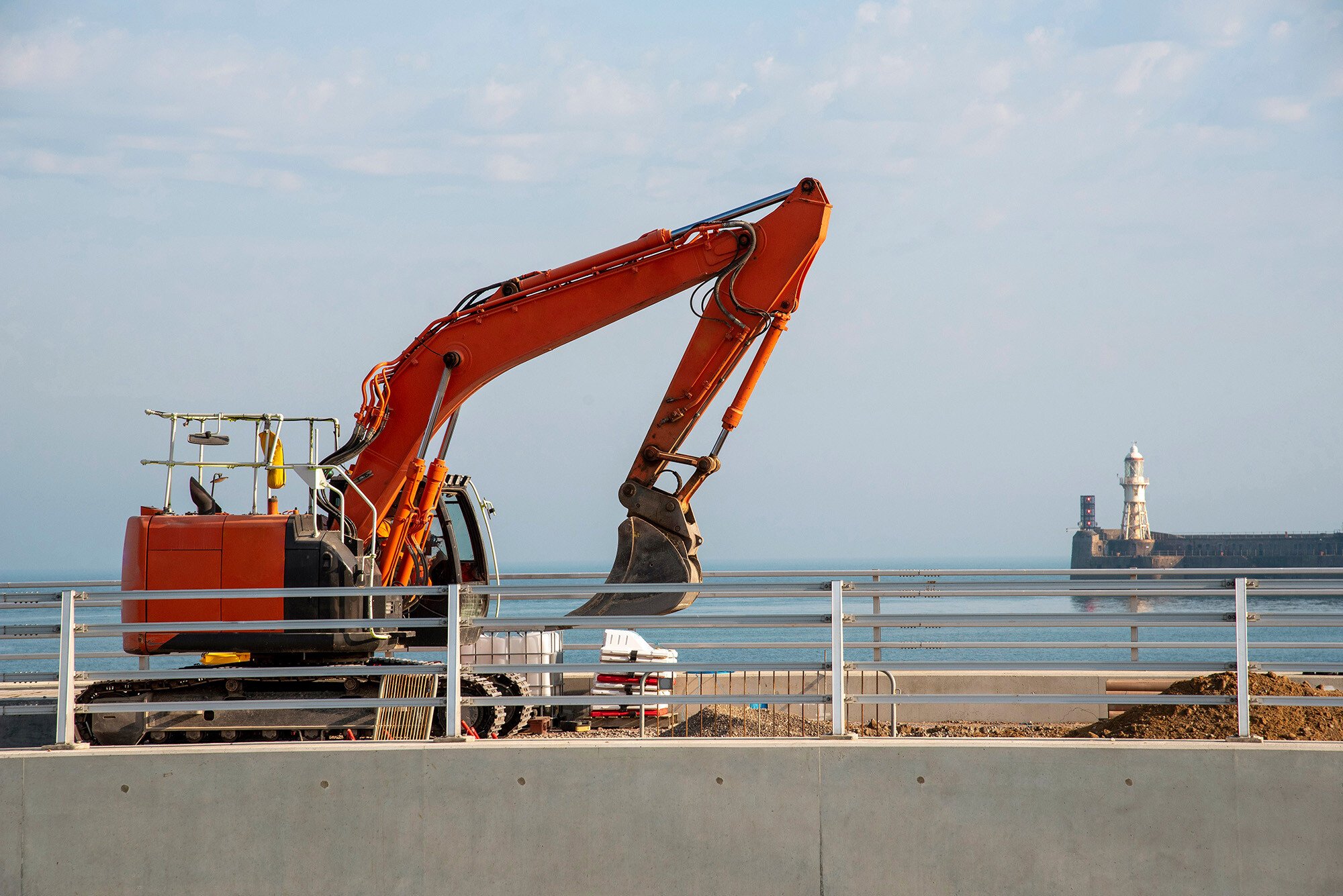
From compact skid steers and mini-excavators to massive dozers and off-highway trucks, construction machines come in all shapes and sizes, each built for a specific job, each with its own demands. What do they all have in common? A cab where the operator spends long hours, often in extreme conditions.
That’s where HVAC for construction equipment plays a critical role. Heating and air conditioning systems aren’t just about comfort, they're essential for safety, keeping workers focused, and ensuring equipment stays up and running. They also need to be cost-effective - especially for high-volume vehicle categories where margins are tight. But not all HVAC systems are created equal. The design and performance requirements can vary significantly depending on the machine type, cab configuration, and work environment.
Take a look inside the cab to explore how climate control systems are engineered differently for various types of construction machinery, and what they need to have in common to meet the demands of the job.
Different Machines, Different HVAC Needs
Every machine has its role and its own set of climate control requirements. From compact equipment that squeezes into tight spaces to heavy-duty machines that operate in the most demanding conditions, HVAC design must adapt to the equipment’s size, use, and operator needs. Let’s break it down.
- Compact equipment
- Mid-range machines
- Heavy-duty equipment
Compact Equipment: Small Cabs, Big Expectations
Compact machines like skid steers, backhoes, and mini-excavators are used across a wide range of job sites, often with tight, enclosed cabs. HVAC systems for these vehicles need to deliver reliable performance in a limited space. That means components must be compact, energy-efficient, and easy to maintain without sacrificing airflow, filtration, or temperature control. In smaller cabs, even slight changes in performance can have a big impact on operator comfort.
Mid-Range Machines: Versatility Meets Durability
Between compact equipment and heavy-duty machines are mid-range vehicles such as telehandlers and excavators. These machines are used across a variety of jobsites, often in shifting environmental conditions, which means their HVAC systems must be both adaptable and dependable.
Machines by major manufacturers like Caterpillar, Bobcat, CNH, Volvo, and Komatsu offer heating and air conditioning systems that are tested to meet demanding standards for heat-load, airflow, vibration, and filtration. Whether operating in dry, dusty zones or humid, high-temperature environments, these systems are built to deliver consistent performance wherever the job goes.
Heavy-Duty Equipment: Handling Extreme Temperatures and Filtering Hazards
On the other end of the spectrum are bulldozers, graders, and off-highway trucks. These machines often run for long hours in punishing conditions. Heating and air conditioning for heavy duty construction equipment must be exceptionally tough, engineered to withstand extreme heat, constant vibration, and high levels of dust and debris.
For example, bulldozer air conditioning units have powerful heat and humidity extractor systems to help keep the operator comfortable inside the cab, even during the peak of summer. But comfort isn’t the only concern. Protecting workers from hazardous airborne particles is just as critical. That’s why strong filtration and cab pressurization are key features in these systems, ensuring a safe, breathable environment on the job site.
Common Ground: What Every HVAC System Must Deliver
While equipment size and function vary widely, certain HVAC fundamentals apply to every construction machine. Regardless of vehicle type, all systems must address three key challenges:
- Extreme temperatures
- Dust and debris
- Constant vibration
- Cost
Extreme Temperatures
From freezing mornings to triple-digit afternoons, construction sites don’t offer climate control. But the cab should. Reliable heating and cooling helps workers stay focused and alert year-round.
Dust and Debris
Construction sites are full of airborne dust and particles. Without proper filtration and cab pressurization, that debris can clog HVAC components, reduce visibility, and create health risks for operators. Robust filtration and pressurization help keep the air inside the cab clean and breathable while protecting system components and extending their lifespan.
Constant Vibration
Uneven terrain, heavy lifting, and continuous hydraulic movement all generate significant vibration that can take a toll on HVAC systems. Ruggedized housings and secure mounting systems protect internal components, making the air conditioner and heater in these vehicles more durable and reliable when running in the field.
Cost
Compact and mid-range construction vehicles are produced in much higher volumes than heavy-duty equipment. These machines are built by the thousands, which places greater pressure on HVAC design to meet strict cost targets. As a result, systems in this category often use molded plastic housings and simplified components to keep their cost competitive without sacrificing durability. In contrast, heavy-duty machines are produced in smaller quantities and may allow for more flexibility in system cost and complexity.
Engineered from the Inside Out
No matter the size or shape of the machine, HVAC systems for construction equipment must be integrated into the design from the very beginning. This ensures each unit can be tested and optimized for the specific conditions it will face in the field. From the shape of the housing to the placement of coils and electronics, every component must fit precisely and perform reliably under pressure.
Ready to dig in? Contact MCC to see how our HVAC for construction equipment is breaking new ground on performance and comfort - both inside and outside the cab.
April 21, 2025